Material cutter
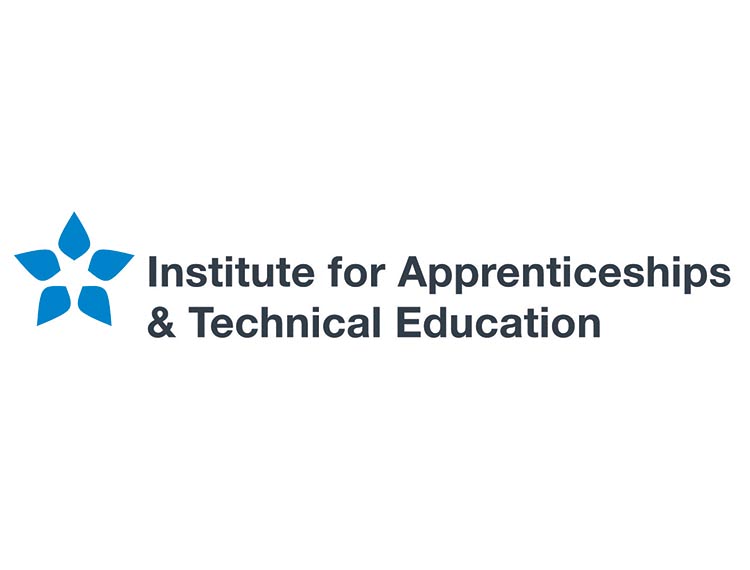
KSBs
Knowledge
K1: The material cutters role, responsibilities, and position within the wider production operation. Back to Duty
K2: Operational insight: types of products produced and types of customers (clothing, home wear, retailers, bespoke). Back to Duty
K3: The end to end production process, quality requirements, deadlines and targets, performance rates (efficiency). Back to Duty
K4: Commercial considerations (efficiency, material cost, production costs). Back to Duty
K5: Health and Safety: Health and Safety at Work Act 1974, Control of Substances Hazardous to Health (COSHH), Manual Handling, Risk Assessments, Personal Protective Equipment (PPE) (Chain mail gloves), machine guards. Back to Duty
K6: Environment and sustainability; Environmental Protection Act 1990, consequences of waste disposal (landfill), energy efficiency. Back to Duty
K7: Work-station ergonomics; posture and positioning whilst cutting. Back to Duty
K8: Workload planning for example scheduling and prioritisation. Back to Duty
K9: The construction, behaviour and appropriate use of different types of materials: canvas, leather, silk, vinyl, woollens. Back to Duty
K10: Material characteristics: quality, colour, pattern, print, pile, correct side. Back to Duty
K11: Material matching techniques for stripes, checks, pattern repeat, print placement. Back to Duty
K12: Material faults and fault tolerances; shading, discoloration, print error, holes, marks. Back to Duty
K13: Component shapes and product parts. Back to Duty
K14: Cutting specifications and instructions; the number to be cut, grain line, size, pairs. Back to Duty
K15: Mathematical techniques for cutting, measuring and calculating meterage. Back to Duty
K16: Measuring tools, equipment and techniques. Back to Duty
K17: Material spreading and transferring information requirements; darts, ease, pocket positions. Back to Duty
K18: Lay planning and pattern placement techniques; manual and machine. Back to Duty
K19: Manual and machine cutting techniques; quality check requirements. Back to Duty
K20: Material cutting machines and equipment: knives, cutting machines, press, scissors; their purpose. Back to Duty
K21: The consequence of machine/equipment mis-use – accidents, machine isolation. Back to Duty
K22: First line preventative maintenance requirements: checking, cleaning, sharpening, or changing blades. Back to Duty
K23: Re-cut request procedures and the re-cut process. Back to Duty
K24: Continuous improvement techniques: lean, 6-Sigma, KAIZEN, 5S (Sort, Set In order, Shine, Standardize and Sustain). Back to Duty
K25: Documentation requirements and their purpose: specification sheets, work records, labels. Back to Duty
K26: Verbal and written communication techniques. Back to Duty
K27: Material cutter terminology: ease, pairs, grain, right side. Back to Duty
K28: Team working techniques and benefits. Back to Duty
K29: Equality and Diversity in the workplace. Back to Duty
Skills
S1: Read, interpret, and follow information for example work instructions, material specifications. Back to Duty
S2: Prepare the work area for cutting materials. Back to Duty
S3: Maintain the work area. Back to Duty
S4: Follow health and safety regulations, legislation and procedures; PPE, manual handling, lifting procedures and ergonomic practice. Back to Duty
S5: Follow environmental and sustainability regulations and procedures. Back to Duty
S6: Estimate and calculate material requirements to complete the job. Back to Duty
S7: Select material following specification or instruction. Back to Duty
S8: Inspect materials against specifications and quality standard. Back to Duty
S9: Check lay plan. Back to Duty
S10: Prepare materials for cutting for example lay and spread material. Back to Duty
S11: Select, check and use tools/equipment for the task. Back to Duty
S12: Cut material by hand and/or machine for example band knife, shears, laser. Back to Duty
S13: Check quality of the lay post cut for example waste minimised, grain, component positioning, colour continuity. Back to Duty
S14: Check cut components. Back to Duty
S15: Prepare material for the next stage of the production process for example bundling, labelling. Back to Duty
S16: Identify and segregate material for reuse, recycling and disposal. Back to Duty
S17: Check and clean tools and equipment and sharpen or change blades as required. Back to Duty
S18: Report cutting issues for example material faults, equipment faults shortages, required recuts, lay plan. Back to Duty
S19: Apply continuous improvement techniques. Back to Duty
S20: Communicate with colleagues: verbal. Back to Duty
S21: Enter information – written or electronic. Back to Duty
Behaviours
B1: Prioritises health, safety and the environment, for example follows safe ergonomic practices, ensures safety and welfare of self and others and adopts environmental working practices. Back to Duty
B2: Uses own initiative, for example when dealing with material faults and flaws. Back to Duty
B3: Adaptable and flexible, for example in response to changes in priorities and work deadlines. Back to Duty
B4: Team player, for example keeps others informed, interacts proactively, considers impact of actions on others, and takes account of equality and diversity. Back to Duty
B5: Takes ownership and responsibility, for example seeks to meet quality targets, completes allocated work on time, escalates issues. Back to Duty
B6: Professional, for example polite and courteous, a good timekeeper, has a positive can-do attitude. Back to Duty
Responses