What is the importance of the safe use of tools and equipment?
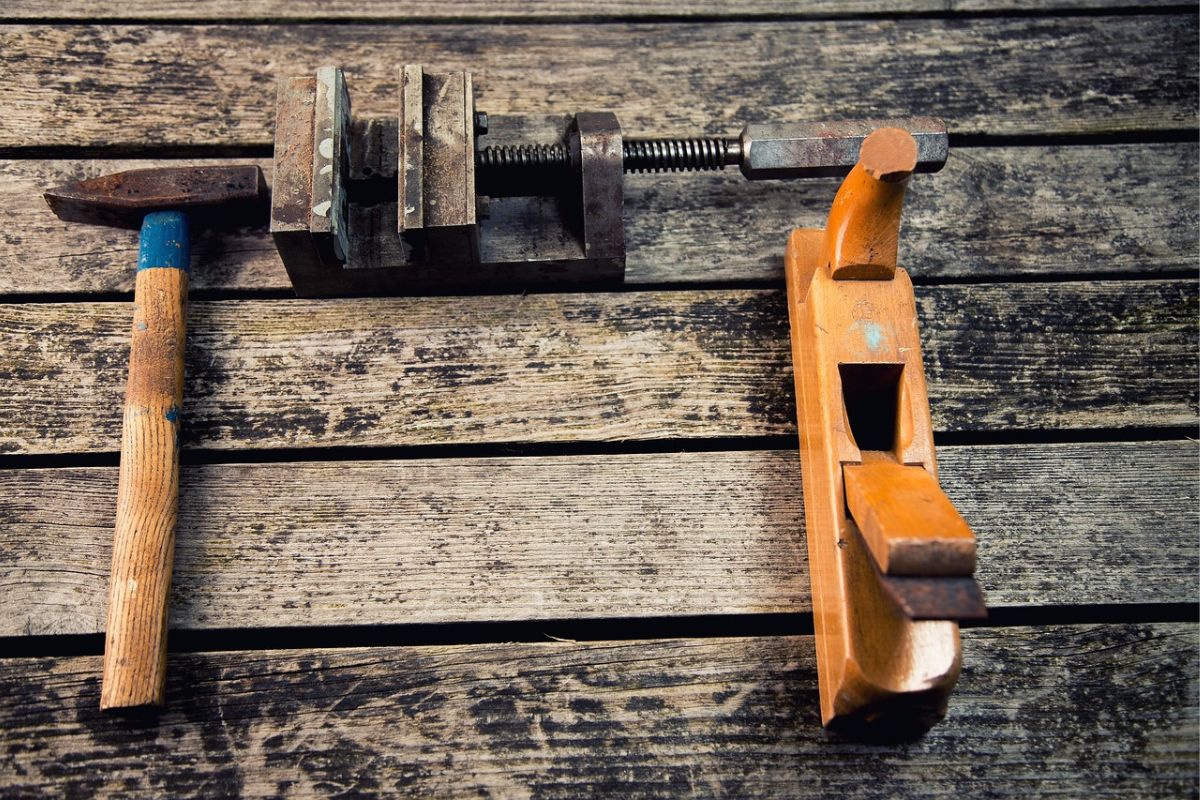
Numerous health and safety accidents or incidents occur due to the equipment being used in the workplace that is improperly designed or is not made for the intended purpose.
Building and construction work in this regard are high-risk industries. Any work process undertaken in these sectors requires high skill and competence to work safely.
This blog post will walk you through in detail the safe handling and usage of work equipment and why is it important to use them safely.
Why Safety Equipment Is Required in the Workplace?
Sometimes we neglect tool and equipment safety. Even when workplaces are made as safe as possible, risks can still be present in one way or the other.
The risks involved in such work operations can damage the head, feet, or other body parts. It is seen that nearly 40% of all work injuries are attributed to manual handling work. Many accidents involving such work include knives and blades which can damage health and safety.
Slips and falls from heights are also significant causes of major workplace injuries. Therefore, employers are required to have a proper ladder setup to avoid these injuries.
Other risks involve falling objects from a height, contact with corrosive chemicals, cuts, or burns. All these issues require special attention while working around them. Employers need to have proper workplace safety arrangements and provide their employees with personal protective equipment to prevent injuries.
Safe Use of Machinery, Equipment & Tools at Work
Employers are required to ensure that all the equipment provide to the workers and employees for use must be safe and not pose any health hazard to its user in the long term. They are also responsible to make sure that the workers using such equipment are skilled and competent to do the work safely.
Numerous legislations revolve around workplace equipment. Provision and Use of Work Equipment Regulations (PUWER) and Control of Vibration Regulations 2005 in particular require that equipment must be:
- Suitable for use
- Maintain for safe use & inspect it regularly
- Examined regularly for wear & tear
- Installed properly for safe work
- Handled carefully to avoid accidents & injuries
Top Reasons for Having Proper Safety Equipment at Work
The below reasons make it even clear why having proper safety equipment is necessary for any business or workplace:
1. Protects Health & Safety
One of the major reasons to have safe work equipment is to ensure the safety and health of those whose work revolves around them. Safety equipment help employers reduce injuries and workers avoid getting injured at work. Using safe equipment at work help prevent health hazards and accidents.
2. Improves Staff Productivity
Using the correct equipment for work not only ensures the safety of the user but also increases staff productivity and efficiency. Especially when a worker is involved in a high-risk task. The right equipment can make the process fast and save you from injuries.
3. Reduces Liability
Getting injured at work can cost businesses expensive costs. Workers getting hurt at work without precautionary measures can pose substantial risks and liability to companies and businesses. Therefore, to avoid these penalties, employers must have the necessary arrangements to avoid these hazards.
4. Creates a Happy Workforce
Workers who feel safe and protected are in turn the happier workforce. A safe and secure workplace leads to lower injuries and ill health cases which means higher employee retention.
Therefore, employers should always look for ways to improve health and safety in their work environment.
5. Improves Safety Awareness Culture
As mentioned above fewer accidents and injuries mean a reduced staff turnover rate which boosts the safety awareness culture within the workplace.
Employers who make health and safety a priority see an upsurge in their workplace than those who do not take it seriously.
Get the Health & Safety Right at Work
It is under the law that employers are required to create and maintain a safe workplace for their employees and anyone involved in the work processes.
One way they can ensure this is by making implementing the right health and safety procedures in their work premises and setting the right expectations to meet their safety goals. Health and safety training in this regard also plays a crucial role which involves numerous training sessions that they can offer their staff.
Some of the vital training courses include work equipment safety training, abrasive wheel training, hand-arm vibration training, lifting operations training, height safety training, and many more relevant courses.
Bottom Line
Health and safety are crucial factors in any work to ensure everyone’s safety at work. So, this is the case when working with the equipment, tools, and machinery at work.
Employers need to be accountable for the safety arrangements at their workplace to ensure that their staff is protected from any health hazards when using equipment at work and provide adequate training to make them competent to work safely.
Responses