Textile manufacturing operative
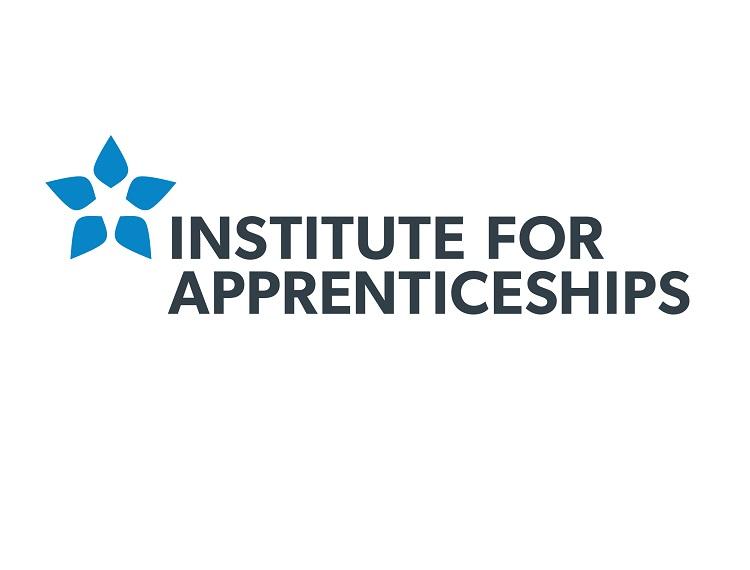
Reference Number: ST0458
Details of standard
Occupational Profile
A textile manufacturing operative is someone who is employed within the textile manufacturing industry and works in an occupation (job role) where they are required to use specific machinery to produce textiles. Typically, this might involve occupations such as carding, spinning, twisting, warping and other roles at the basic/introductory level of the textile manufacturing (this is not an exhaustive list). These individuals are known as ‘operatives’ by the sector and would typically report to a Technician, Supervisor or Line Manager. The key responsibility for a Textile Manufacturing Operative is to ensure the consistency of textile production in a manufacturing facility. The majority of individuals enrolled onto this standard will work within businesses that employ less than 250 employees although, companies that are part of larger organisations are likely to use this programme. Upon completion of this standard, individuals will be competent in specific textile manufacturing operations appropriate to their own occupational role.
Entry Requirements
Individual employers will set the selection criteria and specify the entry requirements applicable to their area of work.
KNOWLEDGE: Individuals must know and understand: |
|
Understand the Industry: |
|
Supply Chain / Customer Base: |
|
Health, Safety & Welfare (Legislation): |
|
Raw Materials: |
|
Quality Standards: |
|
Textile Manufacturing Techniques: |
|
Textile Machinery: |
|
Environment: |
|
SKILLS: The Textile Manufacturing Operative will be able to… |
|
Interpersonal Skills: |
|
Textile Machinery Operations: |
|
Textile Manufacturing Maintenance: |
|
Interpret Data & Instructions |
|
Collaboration & Adaptability: |
|
Time Management: |
|
BEHAVIOURS: The Textile Manufacturing Operative will demonstrate |
|
Ownership & Responsibility: |
|
Precision & Focus: |
|
Mindset: |
|
Communication and service to Customers: |
|
Safety Culture: |
|
Additional information
Duration: Typically, this standard will take 12 to 18 months to achieve
Review: After 3 years or when significant change is required
Qualifications: Typically, employers will look for individuals that already hold appropriate levels of English and Maths however, those without must achieve level 1 English and Maths and take the test for level 2 prior to taking their end-point assessment. For those with an education, health and care plan or a legacy statement the apprenticeships English and maths minimum requirement is Entry Level 3 and British Sign Language qualification are an alternative to English qualifications for whom this is their primary language.
Level:
Level 2
Crown copyright © 2017. You may re-use this information (not including logos) free of charge in any format or medium, under the terms of the Open Government Licence. Visit www.nationalarchives.gov.uk/doc/open-government-licence
Responses