Lift truck and powered access engineering technician
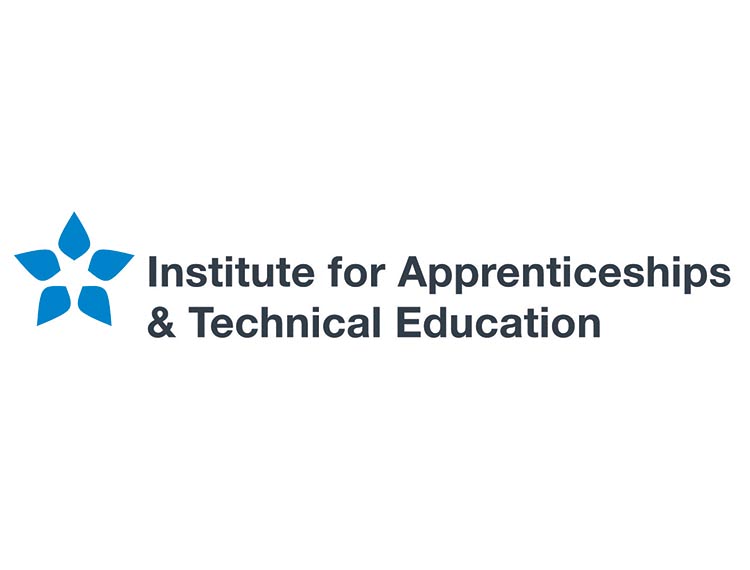
KSBs
Knowledge
K1: Company and customer policies, rules, and safe working procedures when working in different environments Back to Duty
K2: Tools and equipment required for each application within the Lift Truck and Powered Access profession. e.g. jacks and blocks, spanners, socket sets, hammer, screwdrivers (various), pliers, multi-meter, oscilloscope, chain gauge, soldering iron, hacksaw, files, taps, vernier, allen keys, torx bits, straps, torque wrench, oil and lubricants, crimps, stanley knife, drill, goggles, ear protectors, safety boots, gloves and overalls Back to Duty
K3: Fabrication techniques: Soldering / electric & gas welding, electrical, mechanical hydraulic connections & fixings, metal composition, filing, hacksawing, drilling, thread tapping, grinding, and crack detection techniques Back to Duty
K4: The safety aspects of mechanical, electric, and pneumatic tools, lubricants, and specialist equipment Back to Duty
K5: The maintenance, testing and maneuvering purposes of Lift Truck and Powered Access machines for operational purposes Back to Duty
K6: Methodical and systematic techniques for logical fault-finding diagnosis and the verification of functionality and performances of complex Lift Truck and Powered Access machines Back to Duty
K7: Lift Truck and Powered Access machines on-board diagnostics and communication systems and how to set the machine characteristics to meet customer specific requirements within the machines working parameters Back to Duty
K8: The relevant Health and Safety legislation and regulations relating to diagnostics, repair, maintenance and operation of Lift Truck and Powered Access machinery and equipment Back to Duty
K9: Manufacturers’ specifications and customers’ requirements and the process to access, interpret and apply the information gained from them Back to Duty
K10: Principles of electrical, electronic, mechanical, and hydraulic engineering and components and how to apply them to the operation, repair and diagnostics procedures on all types of complex Lift Truck and Powered Access machines Back to Duty
K11: Methods of communication and when and how to apply them appropriately, including customer care techniques Back to Duty
K12: Principles of stock control Back to Duty
K13: How to maintain clear and accurate records, and why this is important Back to Duty
Skills
S1: Carry out safe jacking and blocking procedures; correctly selecting and using lifting and blocking equipment (toe / hydraulic jacks & blocks) Back to Duty
S2: Use correct lifting equipment when removing heavy Lift Truck and Powered Access machine components (chains, slings, shackles) and follow working at height procedures in compliance with appropriate health & safety legislation Back to Duty
S3: Interpret Lift Truck and Powered Access machine electrical, mechanical, and hydraulic schematic diagrams, flow charts and manufacturers’ technical data to verify correct systems functionality Back to Duty
S4: Perform detailed preventative maintenance activities on complex Lift Truck and Powered Access machines in compliance with manufactures’ specifications Back to Duty
S5: Check, diagnose and repair electrical/electronic, mechanical, and hydraulic systems, including:12/24/48/-volt lead acid and lithium-ion batteries Back to Duty
S6: Diagnose and rectify machine charging systems, electrical / electronic wiring / safety circuits Back to Duty
S7: Diagnose and rectify motor control circuits, drive circuits, lift and steer circuits Back to Duty
S8: Test and interpret Control Area Network (CAN Bus) diagnosis Back to Duty
S9: Check diagnose and repair braking and steering systems Back to Duty
S10: Maintain, install & repair machine telematics Back to Duty
S11: Check, repair and diagnose hydraulics components using schematics, pressure gauges, flow meters and on-board computer / laptop programmes Back to Duty
S12: Diagnose and repair hydraulic/electrical proportional control valves and perform breakout calibration of individual valves Back to Duty
S13: Calibrate electronic controllers and recognise the importance of safety devices and systems Back to Duty
S14: Make the required parameter adjustments in compliance with manufactures’ specifications, customer requirements, industry directives and relevant health & safety legislation Back to Duty
S15: Prepare and maintain accurate records of all work undertaken in accordance with company and manufacturer’s requirements Back to Duty
S16: Check and maintain stock to there are no shortages of parts and equipment and no surplus causing undue cost to the business Back to Duty
S17: Politely, keep customers and colleagues informed of progress and any difficulties in relation to work on hand, using the level of technical language appropriate to the audience, offering alternative solutions where required Back to Duty
Behaviours
B1: Safety Culture Conscious: Recognises this is a hazardous industry and adheres to a disciplined approach in maintaining a safe environment Back to Duty
B2: Work Ethic: Positive work principles, reliable, flexible, diligent, and trustworthy Back to Duty
B3: Commitment to industry values: Committed to complying with employer and industry standards Back to Duty
B4: Willingness to learn: Actively involved in undertaking continuous professional development (CPD) Back to Duty
B5: Motivation: Thrives on challenges, uses own initiative, sets targets and achieves goals Back to Duty
B6: Adaptability: Positive to changing situations, technologies and working environments Back to Duty
B7: Personal Responsibility: Driven to succeed, motivated to complete a task Back to Duty
B8: Adheres to Codes of Conduct: Company ambassador, polite; wears corporate work clothing; good personal hygiene; maintains company property; keeps vehicle clean; leads by example, demonstrates “can do!” attitude Back to Duty
Responses