Attracting the next generation of manufacturing talent
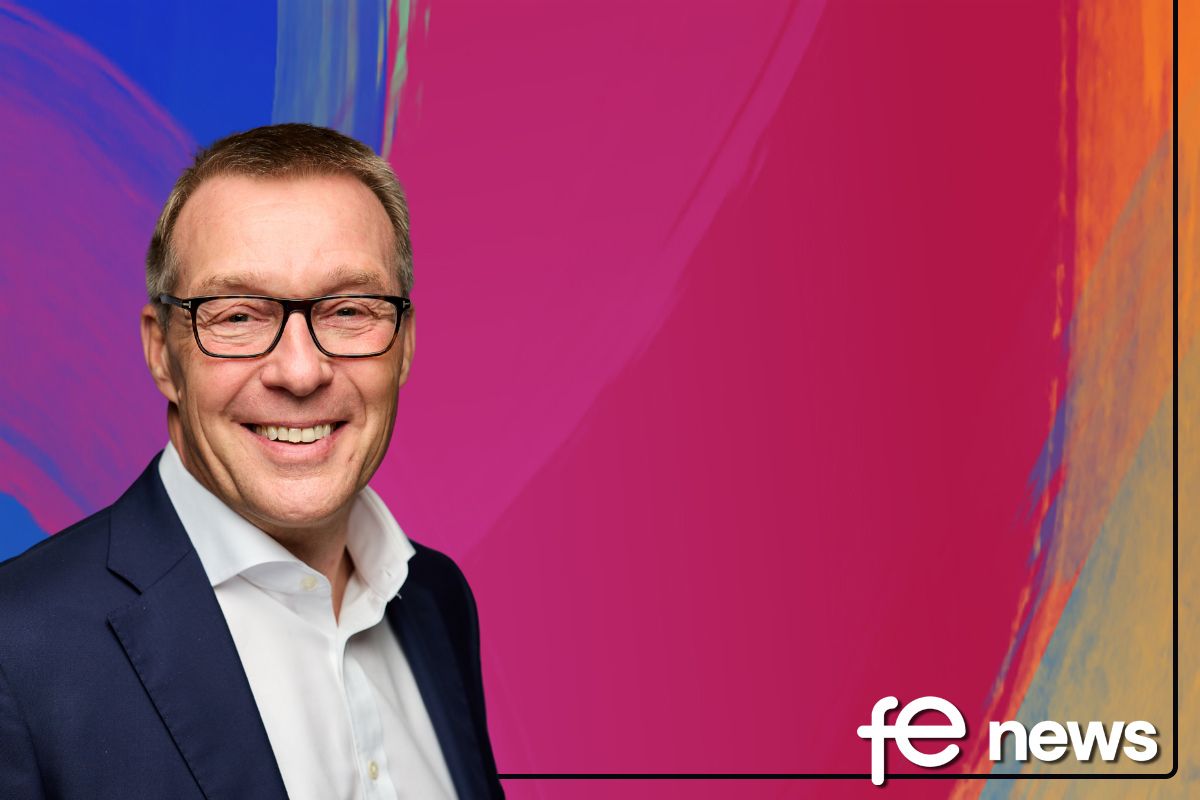
The UK is the ninth largest manufacturing nation in the world as of 2022, providing 2.5 million jobs and an annual output of £183 billion. But despite these promising statistics, the UK manufacturing sector isn’t fulfilling its potential to become a global leader. A major factor preventing this is the growing skills gap — as a result of an ageing workforce and lack of emerging talent. To turn the tide, UK manufacturers need to take a two-pronged approach to attract the next generation of workers.
Last month, the manufacturing sector welcomed the news that students across Britain received the highest grades in STEM A Level subjects than before the COVID-19 pandemic. Despite being the ninth largest manufacturing nation globally as of 2022 (providing 2.5 million jobs and an annual output of £183 billion), the British manufacturing sector is still not considered a global leader. To date, one of the main stumbling blocks has been the widening talent and skills gap due to an ageing workforce and a growing demand for digital skills.
To attract the next generation of workers, the industry needs to prioritise two key areas – implementing innovative technologies and investing in effective education and training programmes. Similarly to engineering, manufacturing needs an image overhaul to attract a younger workforce. By doing so, UK manufacturing can begin to demonstrate that it is supportive of young people and helping them build long-lasting careers.
The role of technology
British manufacturing has been described by some as “lacking innovation”, as hands-on ways of working are opted for over adopting the newest technologies. However, more recently the rise of cloud computing, Artificial Intelligence (AI), IoT, and robotics have transformed the sector for the better. In turn, we’ve seen the creation of new jobs and the evolution of existing roles.
Businesses and their employees are already benefitting from these innovations. For example, enterprise resource planning (ERP) solutions can integrate AI and machine learning capabilities to analyse data and provide solutions for business challenges. In fact they’ve become so effective, that research from MIT last year shows that robotics adoption by manufacturers directly correlates to higher rates of job satisfaction.
Despite fears that cutting-edge technology means less job security, younger generations should focus on the benefits of deploying AI and automation, as it is proving to be a game changer for the industry and workers. Low-code/ no-code solutions are a great example of this as they provide automations that orchestrate human and machine tasks into an end-to-end flow. By automating manual processes on the factory shopfloor that may have once taken hours to complete, employees can now work faster, smarter and are free to add value to whichever area of the business needs it most.
Many manufacturers are still hesitant to embrace new technologies. Too many are still operating on legacy systems and storing their data on-premises with manual processes — rather than in the cloud securely. It’s imperative that more manufacturers engage with trusted technology providers to ensure that their systems are relevant for their industry and accessible to future workers.
Putting the foundations in place to keep up with the technology as it evolves is critical. Collaborating with an industry-specific ERP partner that can tailor platforms and services to meet their needs and elevate their operations is the first step to making this a success. Epicor’s Industry Insights Report 2023 revealed that only 4% of enterprises reported themselves as being based on-premises, while 95% of businesses are overall comfortable with cloud-based business solutions. This highlights the large number of companies who have already migrated to the cloud.
Investing in a comprehensive digital transformation strategy is an important part of this process. Not only does this play a key role in talent retention strategies, it will enable companies to grow alongside their workforce as they develop in their careers.
Prioritising education and training
While we’ve seen efforts to make practical STEM subjects more appealing to students (such as the new T-level courses that were introduced since 2020 for 16–19-year-olds), we’re not seeing this impact entry rates into the sector. This is due to several reasons.
Firstly, we need to work closely with government bodies, educational institutions, and even competitors in our sector to encourage young people to consider manufacturing as a viable career path. Part of that is raising awareness of the benefits and promoting the opportunities a job in manufacturing gives people. For instance, as of 2022, the average manufacturing wage is 12% higher than the whole economy.
Secondly, employers must focus on upskilling young people. By working with training providers, we can equip them with the skills tools they need to thrive in today’s digital-first environment. They can also shine a light on the different entry paths to the industry, including apprenticeship schemes, where young people can get hands-on experience while working towards relevant industry qualifications.
Manufacturers also have a role to play in visiting schools, colleges, and universities to show what a future career in manufacturing looks like. Having employees engage with students provides an opportunity for them to share their own passion and experiences, while demonstrating first-hand how it can offer a rewarding and enjoyable career.
What’s next?
The UK manufacturing industry could consider putting technological innovation at the heart of its hiring strategy as it looks to compete on the global stage. As more new and exciting solutions come to market, UK manufacturers could keep in mind that having a plan in place to invest in the right technologies and ensure resources are allocated to train employees will set them up for success. Ultimately, giving them the opportunity to thrive in today’s competitive and challenging landscape.
By Andy Coussins, Executive Vice President, International, Epicor
Responses